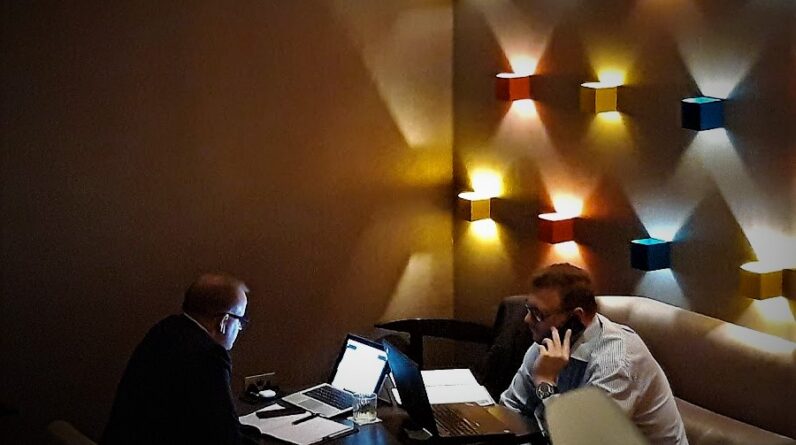
[ad_1]
Business people discussing strategy. Image (C) Tim Sandle
Both COVID-19 and the UK’s exit from the European Union (Brexit) have had a lasting impact on the profitability of businesses. In particular, the manufacturing sector has been heavily impacted due to the UK’s withdrawal from the single market and the subsequent restrictions on imports and exports.
Despite these issues, it appears that many manufacturers are optimistic at least in the short term, and a recent government business survey shows signs of improvement. Manufacturers stand as the most confident of all businesses, with almost a quarter expecting to see turnover increase. This is reflective of actual performance, with manufacturing being placed second to information and communications when it comes to increased turnover (up until June 2023).
Can the situation be improved further? Digital Journal heard from cable assemblies manufacturer GTK in terms of how manufacturers stay afloat in today’s turbulent landscape.
Streamlining processes
With production and supply chain efficiency stalling after Brexit and COVID-19 lockdowns, businesses need to find new ways to streamline their processes. One way to ensure more efficient production is to invest in better machinery and performance solutions.
Updating systems is a significant investment, yet it can reduce overall costs. New technology allows for quicker production, less waste and fewer workers. Investing in new technology or even simple updates for current machinery, connectivity solutions or production processes can help streamline your workflows, saving time and money.
Matt Eden, Engineering Director at GTK explains: “Having the option to automate time-consuming processes for high-volume work is important for business efficiency and profitability. We recommend that manufacturers who produce custom items have facilities that combine human customisation and process automation. For example, we have machinery that automates repetitive processes like wire cutting, stripping and crimping; however, our people are heavily involved in our custom production elements, like lacing and forming of cable looms.”
Maintaining supply chains
Supply chain disruptions as a result of both Brexit and enforced lockdowns had a negative impact on manufacturing output. This dip in production levels presented a serious problem for many businesses, with the majority searching for ways to adapt to our new normal.
Increased red tape surrounding imports and exports is causing frustration for many companies who trade overseas or who require materials from outside the UK. If international companies close their branches in the UK, this may present issues further down the line when they are faced with paperwork and barriers to smooth, fast trade.
Businesses are being forced to adapt to these new supply chains in order to thrive in this new climate. Paul Dearman, Head of Business Development at GTK, recommends that business leaders create strategies tailored to overcoming these challenges: “While we’ve had this in place for a few years, our Core Material Strategy has allowed us to mitigate supply chain issues caused by these recent events. We keep commonly used components and their associated tooling stocked in high volumes, so we can use these components in our builds without having to go through the red tape repeatedly .It’s not too late for businesses to put strategies in place that can create a workaround for these issues, whether that’s holding bulk stock, using alternative parts or working with local suppliers.”
Skills shortages
Free movement between the UK and EU ended with Brexit, with EU citizens now required to prove their settlement status to remain in the country. It’s estimated that this has created a shortage of around 330,000 workers in Britain.
The current points-based immigration system also limits the acquisition of skilled workers in the UK, with those wanting to move to the UK required to achieve at least 70 points through their qualifications and salary. They must also have the ability to speak English.
Immigrants were also one of the groups disproportionately affected by the pandemic, causing a knock-on effect for businesses attempting to recruit further skilled workers. The Workforce Institute at UKG discovered that manufacturers at frontline facilities report being understaffed 38 percent of the time.
Some manufacturers are attempting to address this skills shortage by implementing automated processes. And while automated processes can help make jobs easier, they can’t replace the large number of staff needed to carry out work that technology can’t replicate. Ultimately, automation should be viewed as a way to assist current staff but should not reduce the overall hiring frequency within a company.
By streamlining services, implementing tailored strategies and combating skills shortages with automated systems, businesses can build a plan to avoid the lasting effects of both Brexit and COVID-19.
[ad_2]
Source link